Micro Channel Aluminum Flat Tube, also known as Micro Channel Condenser Tube, Multi-Port Extrusion (MPE) tube is a thin-walled, porous, flat tube-like aluminum profile that plays an important role in automotive heat exchange systems. It usually has multiple channels, which can enhance the heat transfer rate and surface area, effectively improving the heat exchange efficiency. It is widely used in the condenser and evaporator of automobile air conditioning system, and the radiator and heat exchanger of engine cooling system.
Product categories of microchannel aluminum tubes
- Aluminium Micro-channel Tube
- Width: 8-60mm
- Height: 1-5mm
- Wall thickness:0.15mm-0.6mm
- Aluminium Multi-Port Tube
- Width:50-250mm
- Height: 1.5-25mm
- Number of holes:9-56
- Parallel Flow Aluminium Flat Tube
- Width: 50-250mm
- Height: 2-30mm
- Wall thickness:0.15mm-0.6mm
- Zinc-coated Aluminum Tube
- Composition: Zinc powder
- Zinc spraying thickness:5g/m2-15g/m2
- Characteristics: Improvement of corrosion resistance
- Pre-Flux Coated Aluminium Tube
- Composition:Flux (K1-3A1F46)
- Flux thickness: 8g/m2-25g/m2
- Characteristics:No additional brazing required
- Si Flux Coated Aluminum Tube
- Composition: Si flux-66.6%, Silicon Powder-33.3
- Flux thickness: 10-15±2g/m2
- Features: Available bare foil fins
- Large Multi-channel Aluminum Tube
- Alloy: 1060,1100,3003,3102
- Temper:O,H112
- Application: Cooling of new energy power battery
- Double Row Joint Multi-channel Flat Tube
- Alloy: 3003,3102
- Temper: O,H112
- Surface:Mill Finished
- Extruded Alu Harmonica-shaped Tube
- Alloy: 3003
- Use: Intercooler, oil cooler, condenser
- CNC Aluminum Extrusion Battery End Plate
- Alloy: 6061, 6063
- Surface: anodized, polished, milling process
- Application: EV battery module
- Dimple High Frequency Welded Aluminum Tube
- Product:Called aluminum dimple flat tube
- Alloy: 4343/3003/7072, 4343/3003/4343
- Processing: High frequency welding
Hot selling alloys for microchannel aluminum tubes
- 1050 /1060 Parallel Flow Aluminum Flat Tube
- High purity aluminum applications
- High ductility
- Good machinability
- 1100 Aluminum Water-Cooled Micro Channel Tube
- 99% aluminum content
- Good corrosion resistance
- Good machinability
- 3003 Extruded Harmonica Alu Tube
- Al-Mg alloy
- Excellent corrosion resistance
- Good welding properties
- 3102 Zinc-coated Alu Micro Channel Tube
- Al-Mg alloy
- Good thermal conductivity
- Excellent welding properties
- 6061 High Performance Large Multi-channel Alu Tube
- High strength and rigidity
- Excellent mechanical properties
- Good corrosion resistance
- 6063 Large Multi-channel Alu Tube
- Moderate strength
- Excellent plasticity
- Good appearance
Microchannel aluminum flat tubes specifications
Alloy | 1050,1060,1070,1100,3003,3102,6063 |
Temper | H111,H112,T5 |
Width | 8-60mm |
High | 1-5mm |
Chamber Wall Thickness | 0.15mm-0.6mm |
Length | 3m, 6m, delivered in rolls, custom cutting available |
Number Of Stomata | 3-40 |
Spray Zinc Thickness | 5g/㎡-15g/㎡ |
Surface Treatment | flux, galvanized |
Flux Coating Thickness | 8g/㎡-25g/㎡ |
Supply Type | Straight, Rolled |
Production Process | Hot extrusion, Continuous Extrusion |
Standard | GBT 33230-2016,GB/T3190-2008,GB/T6892-2006,GB/T3191-2010 |
Characteristics of aluminum extrusion micro channel tube
- High heat transfer rate
- Low material cost
- Light weight
- Excellent corrosion resistance
- Good pressure resistance
- High precision
- High surface finish
- High recycling value
Applications of parallel flow aluminum flat tube
Aluminum parallel flow microchannel flat tubes are widely used in automotive air conditioning system condensers, evaporator heat exchangers, engine radiators and traditional refrigeration for home air conditioners, refrigerators and other fields. Including but not limited to:
- Evaporator
- Condenser
- Radiators
- Heat exchangers
- Air Conditioner
- Refrigerator
- Freezers
- Gas Oven
Mastar Metal - premier supplier of micro-channel aluminum flat tubes
- High-Performance Alloys: Mastar Metal is committed to developing durable and cost-effective alloys such as 1050, 3003, 3102, 6061, 6063, etc., to meet the demanding requirements of various applications in different projects.
- Comprehensive Molds: With hundreds of sets of extrusion molds in various sizes, Mastar Metal can meet the processing needs of various widths, thicknesses, and hole counts, directly matching existing molds to save on tooling costs.
- Large-Scale Extrusion Capability: Mastar Metal can match extrusion dies with widths of up to 250mm and heights of up to 70mm. High-tonnage micro-channel extrusion machines provide high-quality and strictly toleranced micro-channel tubing.
- Surface Treatment: Utilizing precision galvanizing and flux-assisted welding technology, customized coatings can be tailored to enhance corrosion protection according to your project's specific requirements.
- Precision Tolerance: Mastar Metal's micro-channel aluminum tubes strictly adhere to standard tolerances and employ high-speed cutting technology to ensure consistent lengths, facilitating easy insertion of fittings and maximizing convenience in subsequent production processes.
- Quality Control: All outgoing micro-channel aluminum tubes undergo rigorous process control and are subjected to salt spray tests of over 750 hours, ensuring that the supplied tubing is of high quality.
Detailed data of Mastar Metal microchannel aluminum flat tube
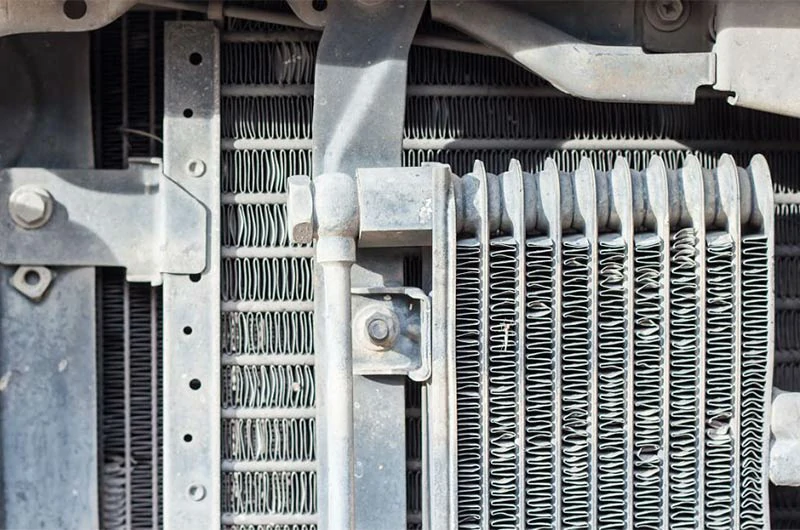
- Chemical composition
- Surface treatment
- Dimensional tolerance
- Straightness
Element | 1050 | 1060 | 1070 | 1100 | 3003 | 3102 | 6061 | 6063 |
Si | 0.25% | 0.25% | 0.20% | - | 0.60% | 0.40% | 0.40-0.8% | 0.20-0.6% |
Fe | 0.40% | 0.35% | 0.25% | - | 0.70% | 0.70% | 0.70% | 0.35% |
Cu | 0.05% | 0.05% | 0.04% | 0.05-0.2% | 0.05-0.2% | 0.10% | 0.15-0.40% | 0.10% |
Mn | 0.05% | 0.03% | 0.03% | 0.05% | 1.0-1.5% | 0.05-0.4% | 0.15% | 0.10% |
Mg | 0.05% | 0.03% | 0.03% | - | - | - | 0.8-1.2% | 0.45-0.9% |
Cr | - | - | - | - | - | - | 0.04-0.35% | 0.10% |
Zn | 0.05% | 0.05% | 0.04% | 0.10% | 0.10% | 0.30% | 0.25% | 0.10% |
Ti | 0.03% | 0.03% | 0.03% | - | - | 0.10% | 0.15% | 0.10% |
Si+Fe | - | - | - | 0.95% | - | - | - | - |
Other | 0.03% | 0.03% | 0.03% | 0.20% | 0.20% | 0.20% | 0.20% | 0.20% |
Al | 99.50% | 99.60% | 99.70% | 99.00% | Re | Re | Re | Re |
Surface | Coating thickness |
Galvanized | 5g/㎡-15g/㎡ |
Flux | 8g/㎡-25g/㎡ |
Width | Thickness | Wall Thicknesses | Length |
±0. 04mm | ±0. 03mm | ±0. 05mm | ±0. 30mm |
Straightness (side) | Straightness (front) | Twisty |
≤L*0.2% | ≤L*0. 25% | ≤L*0.15% |
Die sheet for Mastar Metal microchannel aluminum flat tubes
- 22mm*4mm-12 Hole
- 25mm*6mm-3 Hole
- 25mm*6mm-3 Hole
- 25mm*6mm-8 Hole
- 25.5mm*3mm-4Hole
- 26mm*6mm-3 Hole
- 27mm*8mm-6 Hole
- 32mm*3.5mm-7Hole
- 32mm*5mm-5Hole
- 32mm*6.4mm-6Hole
- 35.5mm*3mm-6 Hole
- 36mm*3mm-11 Hole
- 38mm*6.5mm-3 Hole
- 38.6mm*7mm-6 Hole
- 39.2mm*4.5mm-10 Hole
- 40mm*5mm-7 Hole
- 40mm*7mm-6 Hole
- 40mm*8mm-7 Hole
- 45mm*4mm-7 Hole
- 47mm*4.5mm-7Hole
- 48mm*5mm-8Hole
- 48mm*9.4mm-8Hole
- 49mm*6.1mm-9Hole
- 49mm*6.9mm-8Hole
- 49.2mm*7mm-8Hole
- 49.5mm*4.5mm-12Hole
- 53mm*5mm15Hole
- 53mm*6.5mm-4Hole
- 53mm*6.5mm-7Hole
- 53mm*7.5mm-16Hole
- 54.7mm*8mm-12Hole
- 56mm*10.5mm-7Hole
- 56mm*10.5mm-9Hole
- 56mm*10.5mm-10Hole
- 57mm*6.6mm-9Hole
- 58mm*4.6mm-10Hole
- 58mm*4.6mm-10Hole
- 58mm*6.5mm-7Hole
- 60mm*4.5mm-15Hole
- 60mm*7mm-9Hole
- 62mm*8mm-11/13Hole
- 62.05mm*6.18mm-12Hole
- 62mm*6mm-10Hole
- 62mm*8mm-11/13Hole
- 62.5mm*6.1mm-12Hole
- 64mm*5mm-11Hole
- 64mm*5mm-13Hole
- 64mm*6mm-14Hole
- 64mm*6.6mm-16Hole
- 64mm*8.1mm-12Hole
- 64mm*8.08mm-10Hole
- 65mm*4mm-10Hole
- 65mm*6.4mm-18Hole
- 65mm*6.4mm-18Hole
- 65mm*6.6mm-10Hole
- 66mm*8mm-11Hole
- 68mm*9mm-15Hole
- 70mm*6.5mm-8Hole
- 70mm*7.8mm-12Hole
- 70mm*10mm-12Hole
- 70mm*10mm-6Hole
- 70mm*10.5mm-12Hole
- 72mm*6mm-16Hole
- 75mm*5mm-8Hole
- 76mm*6.5mm-8Hole
- 80mm*5mm-16Hole
- 80mm*6mm-11Hole
- 85mm*7mm-12Hole
- 90mm*6.9mm-14Hole
- 98mm*11mm-17Hole
- 100mm*6.9mm-15Hole
- 100mm*7mm-12Hole
- 104mm*6.4mm-23Hole
- 104mm*6.4mm-30Hole
- 120mm*4mm-47Hole
Manufacturing process for aluminum microchannels tubes
Microchannel tubes are an essential component of the all-aluminum microchannel heat exchangers used in automotive air conditioning systems. They are the core parts that carry the refrigerant and are typically produced using extrusion methods. Currently, there are two main manufacturing processes for aluminum microchannel tubes: short billet hot extrusion and continuous extrusion from coiled aluminum rod. The specific production processes are as follows:
Extruded Aluminum Microchannel Tubes:
Short billet - Billet heating - Induction heating - Hot extrusion - Zinc/flux/soldering agent coating - Cooling - Eddy current testing - Drying - Coiling - Straightening - Cutting - Inspection
Continuously Extruded Aluminum Microchannel Tubes:
Coiled aluminum rod - Uncoiling - Straightening - Cleaning - Continuous extrusion - Zinc/flux/soldering agent coating - Cooling - Eddy current testing - Drying - Coiling - Straightening - Cutting - Inspection
The production of aluminum microchannel tubes involves multiple disciplines and domains, with high requirements for R&D design and practical production experience. To ensure the production of products with high dimensional accuracy and airtightness requirements, in addition to configuring the appropriate production line equipment, the following key technologies need to be mastered:
- Isothermal and equal-speed extrusion: This includes technologies such as isothermal heating of the extrusion chamber and constant-speed extrusion.
- Online surface zinc spraying process: This involves technologies such as online zinc spraying and control, online detection, defect marking, and control feedback.
- Mold manufacturing process: It requires the development and manufacturing technology of extrusion molds with high dimensional accuracy, wear resistance, and heat resistance.
Aluminum Radiator vs Copper Radiator
As an important component of automobiles, the heatsink plays a crucial role in vehicle cooling performance. The selection of suitable materials is the key to ensuring excellent heatsink performance. The following summarizes the performance requirements of heatsink materials and the advantages and disadvantages of aluminum and copper heatsinks:
Performance Requirements for Radiator Materials:
- Possess good thermal conductivity to effectively transfer heat.
- Have adequate strength and strong corrosion resistance to withstand harsh working environments.
- Exhibit good processability and solderability, facilitating manufacturing and installation.
- Demonstrate economic viability, achieving desirable performance at a reasonable cost.
Copper Radiator
As one of the metals with the best thermal conductivity, copper has long played an important role in automotive heatsinks. However, the high price of copper leads to a higher cost for copper heatsinks. Additionally, automotive heatsinks often face harsh working environments and coolant corrosion, making them prone to leakage issues. To improve corrosion resistance, a tin protective layer is typically coated on the surface of copper heatsinks, but the thermal conductivity of tin, at 65.7 W/(m·K), is only 16.7% of that of copper, which can reduce the heat dissipation efficiency and lead to a decline in thermal performance.
Aluminum Radiator
With the development of automotive technology, the demand for vehicle lightweight has become increasingly urgent. Aluminum heatsinks have gradually become the preferred material to replace copper heatsinks. The advantages of aluminum heatsinks are their light weight, abundant resources, low cost, and good heat dissipation performance. However, aluminum heatsinks face certain difficulties in the soldering process, with higher brazing costs, and relatively poorer corrosion resistance, generally requiring zinc spraying or pre-coating with flux treatment.
Radiator Core | Aluminum Radiator | New Copper Radiator |
Head width/mm | 432 | 395 |
Height of heat pipe/mm | 550 | 505 |
Heat sink thickness/mm | 0.114 | 0.038 |
Heat Sink Thickness/mm | 0.381 | 0.102 |
Coolant pressure drop/kPa | 4.75 | 4.75 |
Air pressure drop/kPa | 307 | 0.307 |
Net mass of core/kg | 1.67 | 1.56 |
Wet mass of core/kg | 2.04 | 1.89 |
At present, aluminum radiators have been widely used in city cars and light vehicles, but the use of heavy trucks and engineering vehicles and other harsh conditions are still facing certain challenges, this part of the main copper hard brazed radiators in the main, its advantages are more obvious.