Copper and aluminum are the two most commonly used conductive materials in the electrical industry. Copper, with its excellent electrical and mechanical properties, is the ideal material for electrical conduction. Aluminum, on the other hand, offers both good conductivity and low density, making it an excellent conductor for applications such as automotive lightweighting and power transmission.
Due to the galvanic potential difference between copper and aluminum, and the susceptibility to electrochemical corrosion, reliable and safe copper-aluminum connections require effective solutions in both mechanical strength and corrosion resistance.
NO.1 Welding for aluminum and copper
- Welding for aluminum and copper
- Copper and aluminum conductors can be joined using various welding methods, including flash butt welding, brazing, friction stir welding, and ultrasonic welding. These methods effectively prevent oxidation of the aluminum surface.
The joining of copper and aluminum busbars primarily involves two methods: lap joint and butt joint. Flash butt welding and friction stir welding, due to their unique heating and plastic deformation mechanisms, typically employ butt joints, directly fusing or plastically deforming the end faces of two conductors. Conversely, brazing and ultrasonic welding are more suitable for lap joints, where a filler metal or ultrasonic vibrations are applied to the overlapping surfaces to create a bond. This connection method offers advantages in specific applications, such as when conductor thicknesses vary or increased joint strength is required.
Flash butt welding
Flash butt welding offers a robust method of joining aluminum and copper busbars through metallurgical bonding. This process results in a Cu/Al intermetallic compound at the interface, providing exceptional mechanical and electrical properties. Notably, it exhibits the highest tensile strength among the four welding methods, coupled with low welding resistance and minimal temperature rise, making it ideal for copper-aluminum connections. However, due to stringent production environment requirements, challenges in dimensional control, and environmental concerns, flash butt welding is generally not recommended for applications where it is not strictly necessary.
Friction stir welding (FSW)
Friction stir welding is a solid-state joining process. During Friction Stir Welding(FSW), a cylindrical tool with a specially designed shoulder and pin is rotated and inserted into the workpiece. The frictional heat generated plasticizes the material. As the tool traverses along the joint line, the plasticized material is mechanically stirred and consolidated by the tool, resulting in a solid-state bond between dissimilar metals such as copper and aluminum.
Tests have shown that FSW offers excellent tensile properties and low joint resistance, making it a reliable joining method. The process is simple and suitable for welding aluminum alloys in the 1000, 6000, and 8000 series, demonstrating high efficiency and stability in production. Therefore, FSW is a promising technique for joining copper and aluminum.
Ultrasonic welding
Ultrasonic welding joins copper and aluminum conductors by combining the high-frequency vibration of a sonotrode and the pressure of a welding head. This method is widely used for connecting wires to terminals and can achieve low electrical resistance and high bonding strength.
Test results show that ultrasonic welding has lower contact resistance and temperature rise, but the bonding strength may be lower. For thinner copper and aluminum busbars, ultrasonic welding is reliable, but for thicker ones, the energy of the welding equipment may be insufficient, leading to incomplete welding and reduced bonding strength.
Brazing
Brazing aluminum and copper requires careful consideration of their different melting points (copper: 1083°C, aluminum: 660°C). To ensure only the brazing filler metal melts and not the base metals, appropriate flux and brazing alloy (melting point between 850-900°C) should be used. When brazing aluminum and copper, all components must be clean. Surfaces can be cleaned with a wire brush or sandpaper before heating and a flux should be applied to prevent oxidation and contamination. The flux not only prevents surface oxidation but also promotes heat transfer, ensuring a strong bond during the brazing process.
Due to the different metallic properties of copper and aluminum, several issues need to be considered during welding:
1.Copper and aluminum have different coefficients of thermal expansion and thermal conductivity. During heating, the amount of expansion differs. If heated slowly for too long, the difference in expansion will be greater. Therefore, it is necessary to control the heating of the welding surface and the welding time during the welding process.
2.The welded joint obtained by the composite welding of dissimilar materials of copper and aluminum has relatively high brittleness, and brittle phases are easily generated during the welding process. Due to the formation of copper-aluminum intermetallic compounds at the joint, mainly copper aluminide, brittle compounds are generated at the copper-aluminum weld, which can easily lead to a decrease in the strength of the weld.
3.The melting points of copper and aluminum differ greatly by about 400°C. During welding, it is easy to have a situation where aluminum has melted but copper has not been fully penetrated. Therefore, during welding, it is usually necessary to directly target copper.
NO.2 Bolted aluminum to copper connections
- Bolted aluminum to copper connections
- Fasteners typically include bolts, nuts, split washers or lock washers.
In bolted connections between copper and aluminum, copper salts can corrode aluminum, while aluminum salts do not corrode copper. To minimize the effects of electrochemical corrosion and subsequent aluminum corrosion, the aluminum conductor must always be installed above the copper conductor.
When copper and aluminum bimetallic surfaces have been plated (e.g., with silver, tin, or cadmium), no additional preparation is generally required before joining. However, if the copper or aluminum is bare and unplated, a generous amount of corrosion inhibitor must be applied to both contact surfaces and the joint. Additionally, all unplated contact surfaces (without silver, tin, cadmium, or wax coatings) must be properly cleaned or polished before electrical connection.
The choice of fasteners often depends on the specific metals being joined. For copper and aluminum conductors, aluminum alloy bolt assemblies, tin-plated silicon bronze bolt assemblies, and stainless steel bolt assemblies are commonly used.
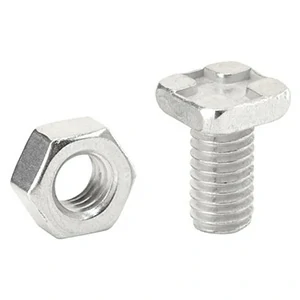
Aluminum fasteners
Aluminum fasteners are commonly used for joining aluminum to aluminum, aluminum to tin-plated aluminum, aluminum to tin-plated copper, and tin-plated copper to tin-plated aluminum.
Standard commercial aluminum bolts are typically made of 2024-T4 alloy, but their copper content can lead to galvanic corrosion, making them unsuitable for outdoor electrical applications. 6061-T6 aluminum alloy offers comparable strength to 2024-T4 but has better corrosion resistance, making it the preferred choice for outdoor electrical applications.
Additionally, using steel flat washers and steel Belleville spring washers can ensure even contact pressure distribution, preventing current concentration and hot spots within the connection.
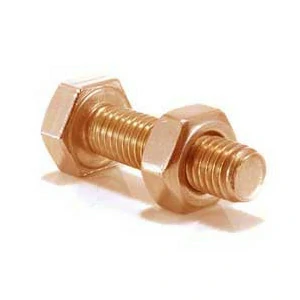
Silicon bronze fasteners
Silicon bronze fasteners are commonly used for joining copper to copper, copper to tin-plated aluminum, tin-plated copper to tin-plated copper, copper to bronze, and bronze to bronze. A crucial consideration when using silicon bronze fasteners is the necessity of stainless steel Belleville washers to effectively generate and maintain the clamping force required for a low-resistance connection.
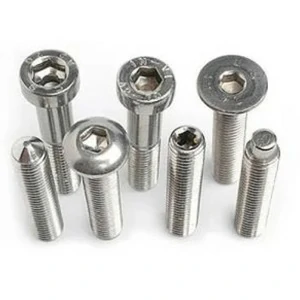
Stainless steel fasteners
The most cost-effective and reliable component choice is 300 series (T18-8) stainless steel. Renowned for its excellent corrosion resistance and strength, stainless steel fasteners are universally recognized as a suitable material for all applications.
It's crucial to note that when bolting components together, the correct torque must be applied to tighten the fasteners. Different bolt sizes have optimal torque values that produce the most reliable, low-resistance connection. Below is a table of optimal torque values for various materials and bolt sizes:
Bolt Size(in) | Aluminum(ft/lb) | Silicon-Bronze (ft/lb) | Stainless Steel (ft/lb) |
3/8 | 14 | 20 | 20 |
1/2 | 25 | 40 | 40 |
5/8 | 40 | 55 | 55 |
3/4 | 54 | 87 | 87 |
Additionally, for dissimilar metal connections like copper-aluminum, specific washers such as Belleville washers, flat washers, split lock washers, or star lock washers are required.
The specific type of fastener is selected based on a combination of the mechanical and electrical characteristics of the application. Typically, fasteners do not carry any electrical load; however, selecting certain metal combinations can reduce the likelihood of corrosion while still providing the necessary mechanical strength to maintain joint integrity.
Summarize
In summary, joining copper and aluminum is crucial for both electrical and mechanical applications.
Welding and bolting offer distinct advantages and disadvantages, and the optimal method depends on the specific requirements of the application.
Welding techniques, such as flash butt welding, friction stir welding, and ultrasonic welding, provide excellent joint strength and electrical conductivity.
Bolted connections, on the other hand, require careful attention to prevent galvanic corrosion. Selecting appropriate fasteners and washers is paramount.
In practical applications, the most suitable joining method should be chosen based on specific circumstances to ensure the safety and reliability of the copper-aluminum joint.