Air separation equipment, which separates air into oxygen, nitrogen, and other gases, has extremely high material performance requirements.
Aluminum maintains excellent toughness and strength under low-temperature conditions. Its surface forms a natural oxide film, providing excellent corrosion resistance. Additionally, its superior thermal conductivity helps improve heat exchange efficiency and shorten the separation process. Therefore, aluminum has become an indispensable material in air separation systems. As a professional aluminum supplier, Mastar can provide a complete set of solutions for air separation equipment.
Overview: aluminum in air separation units (ASUs)
Air Separation Units (ASUs), as extensive systems for separating air into oxygen, nitrogen, and other gases, rely heavily on aluminum. Aluminum components such as plates, tubes, reducers, elbows, and end caps are widely used. Given the primary function of ASUs in gas separation and transportation, aluminum tubes are particularly essential. These tubes vary significantly in diameter, from small-bore instrumentation lines to large-diameter main pipelines.
Generally, small-diameter aluminum tubes are used in instrumentation piping and control systems where flow rates are relatively low. Large-diameter aluminum tubes are typically employed in main pipelines, connections between large tanks or equipment, and other components that need to handle high flow rates. These tubes often have thicker walls to ensure strength and pressure resistance.
For large-diameter aluminum tubes, extrusion can be a challenging and costly manufacturing process. Straight-seam welded tubes often have limited diameter capabilities and may compromise on strength.
Spiral welding is a highly suitable production method. In particular, 5052 and 5083 aluminum alloys, due to their excellent corrosion resistance, low-temperature performance, weldability, and lightweight properties, are ideal for ASU applications.
Spiral welded aluminum tubes for air separation units
- Spiral welded aluminum tubes are produced by spirally winding an aluminum strip into a tubular blank, then welding it along the helical seam. The weld is helical, distributed on the outer wall of the tube. Due to their excellent corrosion resistance, low risk of cracking, and high strength, they are particularly suitable for Air Separation Units.
- Popular Alloys: 5052, 5083
Mastar spiral welded aluminum pipe production range
Alloy | 5052,5754,5083,5a05 |
State | O,H111,H112 |
Outer diameter | 312-1628mm |
Length | 12m |
Standard | GB/T 11433-2009,GB/T 3191-2010,DIN 8625-2 |
Most widely used spiral welded aluminum tubes in asu applications
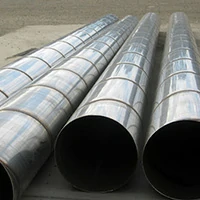
5052 Spiral Welded Aluminum Tubes
With excellent corrosion resistance and high strength, 5052 spiral welded aluminum tubes are ideal for low-temperature and high-humidity environments in ASUs. Their outstanding durability and formability ensure reliability under extreme conditions.
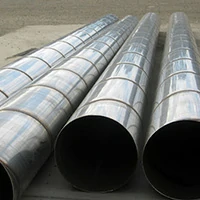
5083 Spiral Welded Aluminum Tubes
Renowned for their exceptional strength and corrosion resistance, 5083 spiral welded aluminum tubes are particularly suitable for high-pressure and harsh environments in ASUs. They offer superior performance and durability under extreme conditions.
Advantages of spiral welded aluminum tubes
High Strength: The weld seam of spiral welded aluminum tubes is subjected to less stress, resulting in higher strength and impact resistance compared to straight-seam welded tubes.
Low Cracking Risk: The helical weld seam distributes stress more evenly, reducing the risk of weld cracking.
High Production Efficiency: Continuous production using aluminum coil strips allows for individual tube lengths up to 12 meters, increasing production efficiency.
High Material Utilization: The width of the aluminum strip determines the final tube diameter (maximum 1628mm), resulting in high material utilization and cost control.
Strict Tolerances: 12-meter long spiral welded aluminum tubes have a straightness tolerance of no more than 3mm and an outer diameter tolerance of ±1mm.
Specific applications of spiral welded aluminum tubes in air separation
Low-Temperature Piping Systems: Thanks to their excellent low-temperature performance and corrosion resistance, aluminum fittings are widely used to connect heat exchangers, low-temperature pipelines, and for transporting liquid oxygen and nitrogen, ensuring the safe and efficient operation of Air Separation Units (ASUs).
High-Pressure Gas Transportation: Used for transporting compressed air and other high-pressure gases, their high-pressure resistance guarantees the safe operation of the system.
Instrumentation Piping Systems: Used to connect various pressure sensors, temperature sensors, and other instruments, enabling the measurement of internal parameters of the equipment.
Liquid Oxygen and Nitrogen Tanks: Can be used to manufacture liquid oxygen and nitrogen tanks, and their low-temperature resistance and pressure resistance ensure the safe and reliable operation of the tanks.
Nominal pressure of spiral welded aluminum pipe
Nominal diameter (ID)/mm | Nominal pressure | OD/mm | WA/mm | Length/mm | Theoretical weight/Kg |
300 | PN≤1.0MPa | 312 | 6 | 12000 | 195 |
350 | PN≤1.0MPa | 362 | 6 | 12000 | 226 |
400 | PN≤1.0MPa | 412 | 6 | 12000 | 257 |
450 | PN≤1.0MPa | 466 | 8 | 12000 | 383 |
500 | PN≤1.0MPa | 516 | 8 | 12000 | 424 |
600 | PN≤1.0MPa | 616 | 8 | 12000 | 507 |
700 | PN≤1.0MPa | 716 | 8 | 12000 | 589 |
800 | PN≤1.0MPa | 820 | 10 | 12000 | 840 |
900 | PN≤1.0MPa | 920 | 10 | 12000 | 943 |
1000 | PN≤1.0MPa | 1024 | 12 | 12000 | 1256 |
1200 | PN≤1.0MPa | 1224 | 12 | 12000 | 1503 |
1300 | PN≤1.0MPa | 1324 | 12 | 12000 | 1626 |
1400 | PN≤1.0MPa | 1428 | 14 | 12000 | 2043 |
1500 | PN≤1.0MPa | 1528 | 14 | 12000 | 2187 |
All our spiral welded pipes undergo rigorous burst tests to ensure that product quality meets relevant national standards. Through high-pressure hydrostatic testing (design pressure: 1.0MPa, burst pressure: 5.1MPa, with no cracks found in the weld seam and the pipe bursting from the base material section), we have verified the pressure resistance of our products, ensuring their safe and reliable application in various working conditions.
- Water injection
- Pressurization
- Blasting
Mechanical properties of spiral welded aluminum tube
Alloy | Temper | Thickness/mm | Tensile strength Rm/MPa | Elongation Rp0.2/MPa | Elongation after fracture A50mm/% |
5052 | O H112 | >3.00-6.00 | 170-215 | ≥65 | ≥18 |
>6.00-14.00 | ≥19 | ||||
5754 | O H111 | >3.00-6.00 | 190-240 | ≥80 | ≥18 |
>6.00-14.00 | ≥18 | ||||
5083 | O H112 | >3.00-6.00 | 275-350 | ≥125 | ≥15 |
>6.00-14.00 | ≥16 | ||||
5A05 | O H112 | >3.00-6.00 | 270-350 | ≥150 | ≥18 |
>6.00-14.00 | ≥19 |
Aluminum elbows for air separation units
- Aluminum elbows, as crucial components for connecting pipelines, are used to join different directions in piping systems, ensuring smooth gas flow. Common applications include low-temperature piping systems, liquid oxygen and nitrogen pipelines, distillation towers, and molecular sieve adsorption towers.
- Common Alloys: 5052, 5083, 6061
Large-diameter thermally bent aluminum elbows: customized piping solutions
- Ultra-Wide Outer Diameter Range: Our aluminum elbows have an outer diameter range from 55mm to 700mm, covering a wide range of needs from small branch pipelines to large transmission mains, meeting the customized requirements of various complex engineering projects.
- Advanced Thermal Bending Process: Using advanced thermal bending technology, through high-temperature heating and precise control, the wall thickness of the elbow is ensured to be uniform, with no obvious deformation, greatly improving the pressure bearing capacity and durability of the elbow.
- Customized Bending Radius: We can customize elbows with different angles such as 22°, 45°, 60°, 90°, and 180° according to your specific needs, flexibly adapting to various pipeline layouts.
- Smooth Surface and Corrosion Resistance: The surface of the elbow is finely processed, smooth and flat, and can be further subjected to surface treatments such as anodizing, significantly improving its corrosion resistance and extending its service life.
- Customizable Nominal Pressure: As a key indicator of the safe operation of the piping system, we can customize multiple pressure levels such as 0.1MPa, 0.25MPa, 0.6MPa, and 1.0MPa, and precise nominal pressure control ensures the more stable operation of your piping system.
Most popular aluminum elbow
- 45° aluminum elbow
- 60° aluminum elbow
- 90° aluminum elbow
- 180° aluminum elbow
- 45° welding aluminum elbow
- 90° welding aluminum elbow
If bending radius determines the fluid dynamics of a pipe, and surface treatment determines its corrosion resistance, then nominal pressure is the key indicator of the safe operation of a piping system.
Different working conditions have varying pressure requirements for pipes. Our aluminum elbows can be customized to meet your air separation project needs with multiple nominal pressure ratings such as 0.1MPa, 0.25MPa, 0.6MPa, and 1.0MPa, ensuring the safe and reliable operation of your piping system in high-pressure environments. Whether it's low-pressure transportation or high-pressure networks, we can provide customized solutions.
Dimensional table for aluminum alloy elbows
Aluminum elbow size table with nominal pressure 0.1MPa
OD mm | WA mm | OD mm | WA mm | OD mm | WA mm | |||
5052 | 5083 | 5052 | 5083 | 5052 | 5083 | |||
55 | 3 | 3 | 158 | 4 | 4 | 400 | 6 | 6 |
70 | 3 | 3 | 200 | 5 | 5 | 450 | 6 | 6 |
90 | 4 | 4 | 250 | 6 | 6 | 500 | 6 | 6 |
110 | 4 | 4 | 300 | 6 | 6 | 600 | 8 | 8 |
133 | 4 | 4 | 350 | 6 | 6 | 700 | 8 | 8 |
Aluminum elbow size table with nominal pressure 0.25MPa
OD mm | WA mm | OD mm | WA mm | OD mm | WA mm | |||
5052 | 5083 | 5052 | 5083 | 5052 | 5083 | |||
55 | 3 | 3 | 158 | 4 | 4 | 400 | 6 | 6 |
70 | 3 | 3 | 200 | 5 | 5 | 450 | 6 | 6 |
90 | 4 | 4 | 250 | 6 | 6 | 500 | 8 | 8 |
110 | 4 | 4 | 300 | 6 | 6 | 600 | 8 | 8 |
133 | 4 | 4 | 350 | 6 | 6 | 700 | 8 | 8 |
Aluminum elbow size table with nominal pressure 0.6MPa
OD mm | WA mm | OD mm | WA mm | OD mm | WA mm | |||
5052 | 5083 | 5052 | 5083 | 5052 | 5083 | |||
55 | 3 | 3 | 158 | 4 | 4 | 400 | 8 | 8 |
70 | 3 | 3 | 200 | 5 | 5 | 450 | 8 | 8 |
90 | 4 | 4 | 250 | 6 | 6 | 500 | 8 | 8 |
110 | 4 | 4 | 300 | 6 | 6 | 600 | 8 | 8 |
133 | 4 | 4 | 350 | 6 | 6 | 700 | 8 | 8 |
Aluminum elbow size table with nominal pressure 1.0MPa
OD mm | WA mm | OD mm | WA mm | OD mm | WA mm | |||
5052 | 5083 | 5052 | 5083 | 5052 | 5083 | |||
55 | 3 | 3 | 158 | 4 | 4 | 400 | 8 | 8 |
70 | 3 | 3 | 200 | - | 5 | 450 | 8 | 8 |
90 | 4 | 4 | 250 | 6 | 6 | 500 | 8 | 8 |
110 | 4 | 4 | 300 | 6 | 6 | 600 | - | 8 |
133 | 4 | 4 | 350 | 6 | 6 | 700 | - | 8 |
Aluminum reducing tube for air separation units
- Aluminum reducing fittings, also known as reducers, are used in piping systems to connect pipes of different diameters, ensuring a smooth transition of fluids. With their excellent low-temperature adaptability and corrosion resistance, they are indispensable components in air separation equipment.
- Common Alloys: 5052, 5083
Types of aluminum reducing tube
- Aluminum Transition Cones
An aluminum transition cone is a conical fitting used to connect pipes of different diameters. The conical transition ensures a smooth flow of fluid during the diameter change, reducing resistance.
- Butt-Weld Concentric Reducer
A butt-weld concentric reducer is a fitting used to connect pipes of different diameters. Both ends of the fitting are concentric, meaning the centerlines of both ends are aligned. This allows for a relatively smooth distribution of fluid pressure and velocity as the fluid transitions from a larger to a smaller diameter pipe.
- Butt-Weld Eccentric Reducer
An eccentric reducer is a fitting with different diameters at both ends. One side is flush, while the other side has a radial variation, and the centerlines are not aligned. This type of reducer is typically used in systems where a smooth fluid flow is required.
Advantages of mastar aluminum reducing fittings
- Uniform Wall Thickness: Through rigorous control of the deformation process, the wall thickness of the reducing fitting is ensured to be uniform, enhancing its reliability in high-pressure and complex environments.
- High-Dimensional Accuracy: Precision molds and extrusion forming technology guarantee the dimensional accuracy of the reducing fitting, ensuring product consistency and stability.
- Excellent Surface Finish: Spinning and thermal forming processes provide an excellent surface finish, further improving the fitting's corrosion resistance and aesthetics.
- Customized Production: Reducing fittings of different diameters and lengths can be customized to meet the specific needs of air separation projects, flexibly satisfying the requirements of various application scenarios.
Aluminum reducer size table
Nominal pressure rating: 0.1MPa, 0.25MPa, 0.6MPa, 1.0MPa
OD mm | WA mm | OD mm | WA mm | OD mm | WA mm | |||
5052 | 5083 | 5052 | 5083 | 5052 | 5083 | |||
45*25 | 2.5 | 2.5 | 70*55 | 3 | 3 | 133*90 | 4 | 4 |
45*30 | 2.5 | 2.5 | 90*55 | 4 | 4 | 133*110 | 4 | 4 |
55*30 | 3 | 3 | 90*70 | 4 | 4 | 158*110 | 4 | 4 |
55*45 | 3 | 3 | 110*70 | 4 | 4 | 158*133 | 4 | 4 |
70*45 | 3 | 3 | 110*90 | 4 | 4 |
Aluminum tees for air separation units
- An aluminum tee is a common pipe fitting, shaped like a "T," used to connect three pipes. It is typically used in piping systems where fluid needs to be distributed or merged. Due to its lightweight, corrosion resistance, and good thermal conductivity, it is widely used in air separation applications.
- Common Alloys: 5052, 5083, 6061
Types of aluminum tees
- Equal Tee
An equal tee has three branches of the same diameter.
- Reducing Tee
A reducing tee has three branches of different diameters.
- Y-Type Tee
Z-A Y-type tee has three branches, with two branches on one side and one on the other.
Advantages of aluminum tees in air separation
- Low-Temperature Performance: Air separation equipment operates at extremely low temperatures, and aluminum maintains excellent mechanical properties at low temperatures without becoming brittle.
- Corrosion Resistance: The various gases produced during air separation can corrode equipment, but the corrosion resistance of aluminum effectively protects the equipment.
- Lightweight: Air separation equipment is often large, and reducing the weight of the equipment can lower transportation and installation costs.
- Thermal Conductivity: In heat exchangers and other equipment, aluminum tees can improve heat transfer efficiency.
Aluminum alloy end caps for air separation units
- An aluminum alloy end cap is a common closure component used for containers, primarily for gas storage tanks and the ends of pipelines. End caps are typically manufactured using spinning, stamping, or thermoforming processes, and they are resistant to low temperatures, corrosion, and easy to process.
- Common Alloys: 5052, 5083
Why choose aluminum alloy end caps for air separation units?
Lightweight: Aluminum alloys have a lower density, which reduces the overall weight of the equipment, lowering transportation and installation costs.
Easy Machinability: Aluminum alloys are easy to form and machine, suitable for various manufacturing processes such as spinning, stamping, and thermoforming. This results in high production efficiency and the ability to meet the needs of cryogenic equipment for end caps of various sizes and shapes.
Corrosion Resistance: Cryogenic equipment often handles oxygen, nitrogen, and other gases, which can be corrosive. Aluminum has excellent corrosion resistance, and when anodized, it can significantly extend the service life of the end cap.
Good Mechanical Properties: Aluminum alloy end caps have sufficient strength and toughness to withstand the high pressure, low temperature, and other complex conditions in cryogenic equipment, ensuring safe operation of the equipment.
Dimensional table of aluminum alloy head
Aluminum head size table with nominal pressure 0.1MPa/0.25MPa
OD mm | WA mm | OD mm | WA mm | OD mm | WA mm | |||
5052 | 5083 | 5052 | 5083 | 5052 | 5083 | |||
80 | 3 | 3 | 300 | 4 | 4 | 700 | 4 | 4 |
100 | 4 | 4 | 350 | 4 | 4 | 800 | 4 | 4 |
125 | 4 | 4 | 400 | 4 | 4 | 900 | 5 | 5 |
150 | 4 | 4 | 450 | 4 | 4 | 1000 | 5 | 5 |
200 | 4 | 4 | 500 | 4 | 4 | 1200 | 6 | 6 |
250 | 4 | 4 | 600 | 4 | 4 |
Aluminum head size table with nominal pressure 0.6MPa
OD mm | WA mm | OD mm | WA mm | OD mm | WA mm | |||
5052 | 5083 | 5052 | 5083 | 5052 | 5083 | |||
80 | 3 | 3 | 300 | 5 | 5 | 700 | 8 | 8 |
100 | 4 | 4 | 350 | 5 | 5 | 800 | 8 | 8 |
125 | 4 | 4 | 400 | 6 | 5 | 900 | 8 | 8 |
150 | 4 | 4 | 450 | 6 | 6 | 1000 | 10 | 8 |
200 | 5 | 5 | 500 | 6 | 6 | 1200 | 10 | 8 |
250 | 5 | 5 | 600 | 6 | 6 |
Aluminum head size table with nominal pressure 1.0MPa
OD mm | WA mm | OD mm | WA mm | OD mm | WA mm | |||
5052 | 5083 | 5052 | 5083 | 5052 | 5083 | |||
80 | 3 | 3 | 300 | 6 | 5 | 700 | 10 | 8 |
100 | 4 | 4 | 350 | 6 | 5 | 800 | 12 | 8 |
125 | 4 | 4 | 400 | 6 | 5 | 900 | 12 | 10 |
150 | 4 | 4 | 450 | 8 | 6 | 1000 | 14 | 10 |
200 | 6 | 5 | 500 | 8 | 6 | 1200 | - | 12 |
250 | 6 | 5 | 600 | 10 | 6 |
What to look for when selecting aluminum head?
- Wall Thickness Uniformity: Ensures the strength and safety of the end cap under high-pressure conditions.
- Surface Treatment: Enhances the corrosion resistance of the end cap, especially in extreme environments, through processes such as anodizing.
- Welding Quality: The welding quality between the end cap and the pipe directly affects the sealing performance and service life.
Cooperation cases in the field of air separation units
Mastar's advantages as an aluminum supplier for air separation units
- Diverse Product Range: We offer a wide range of aluminum spiral welded pipes from small to large diameters (312-1628mm), meeting the critical piping needs of cryogenic equipment. Additionally, we provide complimentary aluminum fittings such as elbows, reducers, tees, and end caps to ensure reliable connections throughout the equipment.
- Advanced Manufacturing Processes: Our spiral welded pipes undergo precise welding techniques to ensure high strength and durability. Elbows are produced using hot bending processes, ensuring uniform wall thickness and customizable bending radii. End caps are manufactured using spinning, stamping, and thermoforming processes to guarantee high strength and reliability.
- Superior Material Properties: Our aluminum raw materials comply with EN and ASTM standards and exhibit lightweight, corrosion resistance, and low-temperature performance, making them ideal for the high-pressure, low-temperature, and complex operating environments of cryogenic equipment, extending equipment life and improving operational efficiency.
- Lean Quality Control: Mastar emphasizes the control of key indicators such as weld quality, wall thickness uniformity, and surface treatment, ensuring that every aluminum product meets stringent industry standards, especially in terms of pressure resistance and corrosion resistance.
- Customized Solutions: Mastar has strong customization capabilities and can provide aluminum components with different bending angles, sizes, and surface treatments to meet the specific requirements of cryogenic equipment.
Spiral welded aluminum pipe vs. Straight-seam welded aluminum pipe: key differences
Spiral welded aluminum pipe
- Even Stress Distribution: The helical weld forms an angle with the pipe axis, effectively dispersing stress and reducing the risk of weld cracking.
- High Manufacturing Flexibility: Narrower strip material can be used to produce large-diameter pipes, and the length is unlimited, offering strong adaptability.
- Stable Pipe Quality: High pipe forming accuracy with minimal pipe straightness and outer diameter deviations.
- Longer Welds: The length of the helical weld is 30% to 100% longer, making welding and inspection more challenging.
- Higher Technical Difficulty: Aluminum alloy spiral welded pipes have higher technical requirements and are more difficult to produce.
Straight-seam welded aluminum pipe
- Fewer Welds: Each straight pipe has fewer welds, making the welding process simpler and production costs lower compared to spiral welded pipes.
- Thick-Walled Pipes: Straight-seam welded pipes can produce thick-walled pipes, suitable for applications requiring high wall thickness and pressure.
- Higher Stress Concentration: The stress of straight-seam welded pipes is mainly concentrated at the weld, limiting its adaptability.
- Limited Pipe Outer Diameter: Only aluminum plates of specific width (usually 2500mm) and length can be used. Customizing extra-wide plates significantly increases costs.
- Poor Pipe Forming: Due to limitations in the forming process, it is difficult to control the orality and straightness of straight-seam pipes.
What are the testing standards for spiral welded aluminum pipes?
Common testing standards for spiral welded aluminum pipes include GB/T 11433 shear test, GB/T 3191 mechanical property test, and GB/T 5237.1 surface treatment test. These standards ensure that the weld strength, pipe quality, and corrosion resistance meet the requirements.
Do aluminum alloy spiral welded pipes have a long service life?
Aluminum alloy spiral welded pipes typically have a long service life, primarily due to their excellent material properties and sophisticated manufacturing processes. Aluminum alloys inherently possess excellent corrosion resistance, high strength, and good heat resistance, making spiral welded pipes durable in various cryogenic applications.
Are aluminum alloy spiral welded pipes prone to rusting?
Aluminum alloy spiral welded pipes have excellent corrosion resistance. When their surface is oxidized, a dense oxide film forms, effectively preventing further oxidation reactions. This oxide film has good adhesion and weather resistance, effectively protecting the underlying aluminum alloy from further corrosion.