7150 aluminum alloy is an ultra-high-strength, corrosion-resistant forged aluminum alloy developed in the late 1970s. It is an improved version of 7050, with 10%-15% higher strength and 10% better fracture toughness in the T651 condition compared to 7075. This alloy achieved the balance between high strength and good corrosion resistance for the first time. After heat treatment, 7150 aluminum demonstrates excellent performance in strength, exfoliation corrosion resistance, stress corrosion cracking resistance, fracture toughness, and fatigue strength, making it especially suitable for the aerospace industry.
As a professional aluminum supplier, Mastar customizes aluminum bars according to EN, ASTM, and AMS standards based on customer needs. All materials are strictly tested before shipment, with product quality reports provided as proof of quality.
Popular products of 7150 aluminum bar
- 7150 T77511 extruded bar
- After undergoing solution heat treatment and artificial over-aging, the 7150 T77511 extruded bar offers high strength and excellent exfoliation corrosion resistance. Stress relief through controlled stretching ensures dimensional stability. It is commonly used in critical components such as aircraft wing spars and fuselage frames.
- 7150 T61511 extruded bar
- The 7150 T61511 extruded bar undergoes solution heat treatment with controlled stretching to ensure dimensional stability. Under under-aged conditions, artificial aging enhances formability, making it ideal for aerospace structural components.
What can we offer as a high-quality aluminum rod supplier?
- High-Quality Products: We use premium aluminum rod billets, utilizing precise alloying and heat treatment processes to optimize the product's strength and ductility. We ensure uniform cooling and annealing processes to guarantee high tensile strength and excellent performance.
- Excellent Grain Control: Through reverse extrusion technology, we control cooling rates and perform homogenization treatment. The coarse grain ring is typically controlled to ≤0.5mm, reducing quality defects and ensuring a refined material structure, enhancing product consistency.
- Fast Delivery: With over 10,000 tons of stock, regular sizes can be matched with existing inventory for fast shipment. Our advanced equipment and professional team reduce lead times, providing efficient logistics and ensuring timely delivery.
- Price Advantage: We support both retail and large-scale purchases for metal distributors. We offer discounts and rebate policies for B2B bulk purchasing clients. Our quotes are transparent, ensuring a competitive price for aluminum rods of the same quality.
- Comprehensive Quality Testing: We strictly implement multiple inspection procedures, including tensile strength, elongation properties, ultrasonic testing, and metallographic examination, to ensure that all aluminum rods leaving the warehouse meet AMS, EN, NADCAP, and other standards.
- Detailed Export Packaging: We use high-quality packaging materials, such as wooden crates, slatted boxes, cartons, pallets, plastic coatings, and custom bundles, to prevent rust and corrosion issues during sea transport, ensuring product integrity.
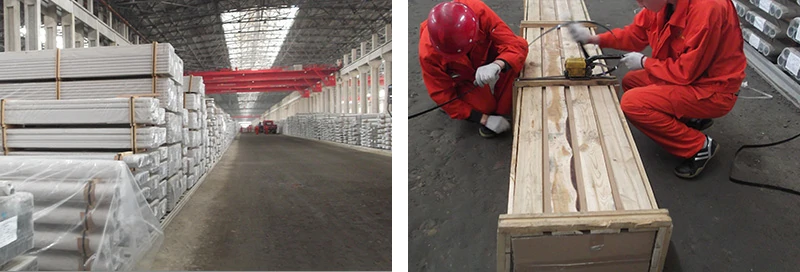
- Complete Documentation: We provide thorough quality testing reports, including raw material certificates, lab test reports, fumigation certificates, specification guides, commercial invoices, and guarantees, ensuring transparency and traceability of every batch.
- Customer Service: We offer comprehensive after-sales support to address all customer concerns. Our experienced technical team provides professional consultations and guidance, establishing a robust customer service system to ensure an outstanding service experience.
Chemical composition of 7150 T77511 extruded bar
Element | Value |
Si | 0.12 |
Fe | 0.15 |
Cu | 1.9-2.5 |
Mn | 0.1 |
Mg | 2.0-2.7 |
Cr | 0.04 |
Zn | 5.9-6.9 |
Ti | 0.06 |
Remarks | 0.08-0.15 Zr |
Others (Each) | 0.05 |
Others (Total) | 0.15 |
Al | Rem |
Physical properties of 7150 T77511 extruded bar
Physical Property | Value |
Density | 2.86 g/cm³ |
Mechanical properties of 7150 T77511 extruded bar
Mechanical Properties | Value |
Proof Strength | 240Mpa |
Yield strength | 620Mpa |
Shear Strength | 430Mpa |
Elongation | 9% |
Hardness | 125 |
Features of 7150 aluminum bar
Ultra-High Strength: After heat treatment, 7150 aluminum bars exhibit significantly higher strength, 10%-15% stronger than 7075 aluminum, making them suitable for high-load aerospace structures.
Excellent Corrosion Resistance: Especially after T77511 heat treatment, the alloy shows superior exfoliation corrosion resistance, making it ideal for harsh environments.
Stress Corrosion Cracking Resistance: The 7150 aluminum alloy, after T77511 treatment, demonstrates excellent resistance to both exfoliation corrosion and stress corrosion cracking, crucial for long-term aerospace applications where materials are exposed to stress and corrosive elements.
Fracture Toughness: Compared to 7050 aluminum alloy, 7150 has higher fracture toughness, making it suitable for structural components that need to withstand extreme loads and impacts, ensuring that the material does not easily fracture under high stress.
Fatigue Strength: 7150 aluminum also has outstanding fatigue strength, particularly in high-cycle fatigue environments, which helps extend the lifespan of critical aerospace components, improving overall reliability.
Good Machinability: Despite medium weldability, 7150 aluminum offers good machinability, maintaining material stability and dimensional accuracy during forming and heat treatment processes.
Best application areas for 7150 aluminum bar
Due to its high strength, excellent corrosion resistance, and superior fatigue performance, 7150 aluminum bars are widely used in the aerospace industry. They are primarily utilized for manufacturing high-strength structural components in large aircraft, such as upper wing structures, fuselage panel beams flanges, fuselage reinforcements, keel beams, fuselage stringers, fuselage frames, fuselage trusses, seat rails, vertical tail joints, and rocket nozzle structures.
EN AW-7150 aluminum rod bar knowledge center
Equivalent grades of 7150 aluminum alloy
- UNS A97150
- AlZn6CuMgZr
- AA7150
- Al7150
Standards for 7150 aluminum rod bar
- AMS4307 - Aluminum Alloy, Extrusions 6.4Zn - 2.4Mg - 2.2Cu - 0.12Zr (7150-T61511) Solution Heat Treated, Stress Relieved by Stretching, Straightened, and Precipitation Heat Treated
- AMS4325 - Aluminum Alloy, Extruded Wide Panel Profiles (7150-T77511) 6.4Zn - 2.4Mg - 2.2Cu - 0.12Zr Solution Heat Treated, Stress-Relieved, Straightened and Overaged
- AMS4345 - ALUMINUM ALLOY EXTRUSIONS 6.4Zn - 2.4Mg - 2.2Cu - 0.12Zr (7150-T77511) Solution Heat Treated, Stress Relieved, and Overaged
7050-T74511 vs 7150-T77511
7050 aluminum alloy, being the third-generation aerospace aluminum, boasts high strength and good corrosion resistance, while 7150 takes this a step further by optimizing the composition and heat treatment process to improve strength, fracture toughness, and exfoliation corrosion resistance. 7150 can be considered an upgraded version of 7050, developed specifically to meet the demand for higher strength and better corrosion resistance in aerospace applications. The key differences are as follows:
- Strength: The strength of 7150-T77511 is about 10%-15% higher than 7050-T74511. 7150, through optimized heat treatment, improves strength while maintaining corrosion resistance, whereas 7050-T74511, though slightly weaker, still offers excellent strength and toughness compared to regular 7000 series alloys.
- Corrosion Resistance: 7150-T77511 shows better resistance to exfoliation corrosion and stress corrosion cracking, making it more suitable for applications exposed to harsh environments over long periods. 7050-T74511 also has good corrosion resistance but is slightly inferior in extreme environments compared to 7150.
- Fracture Toughness: 7150-T77511 has better fracture toughness than 7050, making it ideal for structural components that require high impact resistance. While 7050-T74511 may not match 7150 in fracture toughness, it is still robust enough for most high-load aerospace applications, especially in weight-optimized designs.
- Applications: 7150-T77511 is mainly used in components that endure high stress and corrosion, such as aircraft wings, fuselage stringers, and landing gear. 7050-T74511 is typically used in secondary structures or components with relatively lower stress but still require lightweight properties, such as internal frames and beams.