El cobre y el aluminio son los dos materiales conductores más utilizados en la industria eléctrica. El cobre, con sus excelentes propiedades eléctricas y mecánicas, es el material ideal para la conducción eléctrica. El aluminio, por otro lado, ofrece buena conductividad y baja densidad, lo que lo convierte en un excelente conductor para aplicaciones como el aligeramiento automotriz y la transmisión de potencia.
Debido a la diferencia de potencial galvánico entre el cobre y el aluminio, y la susceptibilidad a la corrosión electroquímica, las conexiones de cobre-aluminio confiables y seguras requieren soluciones efectivas tanto en resistencia mecánica como en resistencia a la corrosión.
NO.1 Soldadura para aluminio y cobre
- Soldadura para aluminio y cobre
- Los conductores de cobre y aluminio se pueden unir utilizando varios métodos de soldadura, incluida la soldadura a tope flash, la soldadura fuerte, la soldadura por fricción y agitación y la soldadura ultrasónica. Estos métodos previenen eficazmente la oxidación de la superficie del aluminio.
La unión de barras colectoras de cobre y aluminio implica principalmente dos métodos: unión traslapada y unión a tope. La soldadura a tope flash y la soldadura por fricción y agitación, debido a sus mecanismos únicos de calentamiento y deformación plástica, generalmente emplean uniones a tope, fusionando directamente o deformando plásticamente las caras de los extremos de dos conductores. Por el contrario, la soldadura fuerte y la soldadura ultrasónica son más adecuadas para las uniones traslapadas, donde se aplica un metal de aporte o vibraciones ultrasónicas a las superficies superpuestas para crear una unión. Este método de conexión ofrece ventajas en aplicaciones específicas, como cuando los espesores de los conductores varían o se requiere una mayor resistencia de la unión.
Soldadura a tope flash
La soldadura a tope flash ofrece un método robusto para unir barras colectoras de aluminio y cobre a través de la unión metalúrgica. Este proceso da como resultado un compuesto intermetálico de Cu/Al en la interfaz, que proporciona propiedades mecánicas y eléctricas excepcionales. En particular, exhibe la mayor resistencia a la tracción entre los cuatro métodos de soldadura, junto con una baja resistencia a la soldadura y un aumento mínimo de temperatura, lo que lo hace ideal para conexiones de cobre y aluminio. Sin embargo, debido a los estrictos requisitos del entorno de producción, los desafíos en el control dimensional y las preocupaciones ambientales, la soldadura a tope flash generalmente no se recomienda para aplicaciones en las que no es estrictamente necesaria.
Soldadura por fricción y agitación (FSW)
La soldadura por fricción y agitación es un proceso de unión de estado sólido. Durante la soldadura por fricción y agitación (FSW), una herramienta cilíndrica con un hombro y un pasador especialmente diseñados se gira y se inserta en la pieza de trabajo. El calor por fricción generado plastifica el material. A medida que la herramienta atraviesa la línea de unión, el material plastificado es agitado mecánicamente y consolidado por la herramienta, lo que da como resultado una unión de estado sólido entre metales diferentes como el cobre y el aluminio.
Las pruebas han demostrado que FSW ofrece excelentes propiedades de tracción y baja resistencia a la unión, lo que lo convierte en un método de unión confiable. El proceso es simple y adecuado para soldar aleaciones de aluminio en las series 1000, 6000 y 8000, lo que demuestra una alta eficiencia y estabilidad en la producción. Por lo tanto, FSW es una técnica prometedora para unir cobre y aluminio.
Soldadura ultrasónica
La soldadura ultrasónica une conductores de cobre y aluminio combinando la vibración de alta frecuencia de un sonotrodo y la presión de un cabezal de soldadura. Este método es ampliamente utilizado para conectar cables a terminales y puede lograr una baja resistencia eléctrica y una alta fuerza de unión.
Los resultados de las pruebas muestran que la soldadura ultrasónica tiene una menor resistencia de contacto y aumento de temperatura, pero la fuerza de unión puede ser menor. Para barras colectoras de cobre y aluminio más delgadas, la soldadura ultrasónica es confiable, pero para las más gruesas, la energía del equipo de soldadura puede ser insuficiente, lo que lleva a una soldadura incompleta y una resistencia de unión reducida.
Soldadura
La soldadura fuerte de aluminio y cobre requiere una cuidadosa consideración de sus diferentes puntos de fusión (cobre: 1083 °C, aluminio: 660 °C). Para garantizar que solo se funda el metal de aporte de soldadura fuerte y no los metales base, se debe utilizar un fundente y una aleación de soldadura fuerte adecuados (punto de fusión entre 850 y 900 °C). Al soldar aluminio y cobre, todos los componentes deben estar limpios. Las superficies se pueden limpiar con un cepillo de alambre o papel de lija antes de calentar y se debe aplicar un fundente para evitar la oxidación y la contaminación. El fundente no solo evita la oxidación de la superficie, sino que también promueve la transferencia de calor, lo que garantiza una fuerte unión durante el proceso de soldadura fuerte.
Debido a las diferentes propiedades metálicas del cobre y el aluminio, se deben tener en cuenta varias cuestiones durante la soldadura:
1. El cobre y el aluminio tienen diferentes coeficientes de expansión térmica y conductividad térmica. Durante el calentamiento, la cantidad de expansión difiere. Si se calienta lentamente durante demasiado tiempo, la diferencia en la expansión será mayor. Por lo tanto, es necesario controlar el calentamiento de la superficie de soldadura y el tiempo de soldadura durante el proceso de soldadura.
2. La unión soldada obtenida por la soldadura compuesta de materiales diferentes de cobre y aluminio tiene una fragilidad relativamente alta, y las fases quebradizas se generan fácilmente durante el proceso de soldadura. Debido a la formación de compuestos intermetálicos de cobre-aluminio en la unión, principalmente aluminuro de cobre, se generan compuestos frágiles en la soldadura de cobre-aluminio, lo que puede conducir fácilmente a una disminución de la resistencia de la soldadura.
3. Los puntos de fusión del cobre y el aluminio difieren mucho en aproximadamente 400 °C. Durante la soldadura, es fácil tener una situación en la que el aluminio se ha derretido pero el cobre no se ha penetrado completamente. Por lo tanto, durante la soldadura, generalmente es necesario apuntar directamente al cobre.
NO.2 Conexiones atornilladas de aluminio a cobre
- Conexiones atornilladas de aluminio a cobre
- Los sujetadores generalmente incluyen pernos, tuercas, arandelas divididas o arandelas de seguridad.
En las conexiones atornilladas entre cobre y aluminio, las sales de cobre pueden corroer el aluminio, mientras que las sales de aluminio no corroen el cobre. Para minimizar los efectos de la corrosión electroquímica y la posterior corrosión del aluminio, el conductor de aluminio siempre debe instalarse sobre el conductor de cobre.
Cuando las superficies bimetálicas de cobre y aluminio se han recubierto (por ejemplo, con plata, estaño o cadmio), generalmente no se requiere preparación adicional antes de unirlas. Sin embargo, si el cobre o el aluminio están desnudos y sin chapa, se debe aplicar una cantidad generosa de inhibidor de corrosión tanto en las superficies de contacto como en la junta. Además, todas las superficies de contacto sin recubrimiento (sin recubrimientos de plata, estaño, cadmio o cera) deben limpiarse o pulirse adecuadamente antes de la conexión eléctrica.
La elección de los sujetadores a menudo depende de los metales específicos que se unen. Para conductores de cobre y aluminio, se usan comúnmente conjuntos de pernos de aleación de aluminio, ensamblajes de pernos de bronce al silicio estañado y ensamblajes de pernos de acero inoxidable.
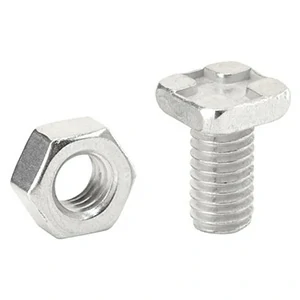
Sujetadores de aluminio
Los sujetadores de aluminio se usan comúnmente para unir aluminio con aluminio, aluminio con aluminio estañado, aluminio con cobre estañado y cobre estañado con aluminio estañado.
Los pernos de aluminio comerciales estándar suelen estar hechos de aleación 2024-T4, pero su contenido de cobre puede provocar corrosión galvánica, lo que los hace inadecuados para aplicaciones eléctricas al aire libre. La aleación de aluminio 6061-T6 ofrece una resistencia comparable a la 2024-T4, pero tiene una mejor resistencia a la corrosión, lo que la convierte en la opción preferida para aplicaciones eléctricas al aire libre.
Además, el uso de arandelas planas de acero y arandelas elásticas Belleville de acero puede garantizar una distribución uniforme de la presión de contacto, evitando la concentración de corriente y los puntos calientes dentro de la conexión.
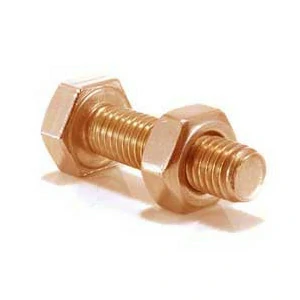
Sujetadores de bronce de silicona
Los sujetadores de bronce de silicio se usan comúnmente para unir cobre con cobre, cobre con aluminio estañado, cobre estañado con cobre estañado, cobre con bronce y bronce con bronce. Una consideración crucial cuando se utilizan sujetadores de bronce de silicona es la necesidad de arandelas Belleville de acero inoxidable para generar y mantener de manera efectiva la fuerza de sujeción requerida para una conexión de baja resistencia.
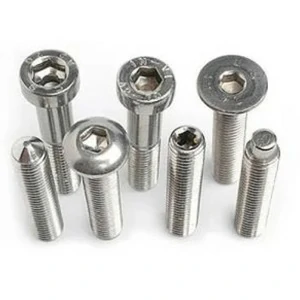
Sujetadores de acero inoxidable
La opción de componentes más rentable y fiable es el acero inoxidable de la serie 300 (T18-8). Reconocidos por su excelente resistencia a la corrosión y resistencia, los sujetadores de acero inoxidable son universalmente reconocidos como un material adecuado para todas las aplicaciones.
Es crucial tener en cuenta que al atornillar componentes, se debe aplicar el par correcto para apretar los sujetadores. Los diferentes tamaños de pernos tienen valores de par óptimos que producen la conexión más confiable y de baja resistencia. A continuación se muestra una tabla de valores de par óptimos para varios materiales y tamaños de pernos:
Tamaño del perno (pulgadas) | Aluminio (ft/lb) | Silicio-Bronce (pies/libras) | Acero inoxidable (pies/libras) |
3/8 | 14 | 20 | 20 |
1/2 | 25 | 40 | 40 |
5/8 | 40 | 55 | 55 |
3/4 | 54 | 87 | 87 |
Además, para conexiones metálicas diferentes como el cobre-aluminio, se requieren arandelas específicas como las arandelas Belleville, las arandelas planas, las arandelas de seguridad dividida o las arandelas de bloqueo de estrella.
El tipo específico de sujetador se selecciona en función de una combinación de las características mecánicas y eléctricas de la aplicación. Por lo general, los sujetadores no llevan ninguna carga eléctrica; Sin embargo, la selección de ciertas combinaciones de metales puede reducir la probabilidad de corrosión y, al mismo tiempo, proporcionar la resistencia mecánica necesaria para mantener la integridad de la unión.
Resumir
En resumen, la unión de cobre y aluminio es crucial tanto para aplicaciones eléctricas como mecánicas.
La soldadura y el atornillado ofrecen distintas ventajas y desventajas, y el método óptimo depende de los requisitos específicos de la aplicación.
Las técnicas de soldadura, como la soldadura a tope flash, la soldadura por fricción y agitación y la soldadura ultrasónica, proporcionan una excelente resistencia de la unión y conductividad eléctrica.
Las conexiones atornilladas, por otro lado, requieren una atención cuidadosa para evitar la corrosión galvánica. La selección de sujetadores y arandelas adecuados es primordial.
En aplicaciones prácticas, el método de unión más adecuado debe elegirse en función de circunstancias específicas para garantizar la seguridad y confiabilidad de la unión de cobre y aluminio.