Cobre e alumínio são os dois materiais condutores mais comumente usados na indústria elétrica. O cobre, com suas excelentes propriedades elétricas e mecânicas, é o material ideal para a condução elétrica. O alumínio, por outro lado, oferece boa condutividade e baixa densidade, tornando-o um excelente condutor para aplicações como redução de peso automotiva e transmissão de energia.
Devido à diferença de potencial galvânico entre cobre e alumínio e à suscetibilidade à corrosão eletroquímica, conexões de cobre-alumínio confiáveis e seguras exigem soluções eficazes tanto em resistência mecânica quanto em resistência à corrosão.
NO.1 Soldagem para alumínio e cobre
- Soldagem para alumínio e cobre
- Os condutores de cobre e alumínio podem ser unidos usando vários métodos de soldagem, incluindo soldagem de topo por flash, brasagem, soldagem por fricção e soldagem ultrassônica. Esses métodos evitam efetivamente a oxidação da superfície do alumínio.
A união de barramentos de cobre e alumínio envolve principalmente dois métodos: junta sobreposta e junta de topo. A soldagem de topo por flash e a soldagem por fricção, devido aos seus mecanismos exclusivos de aquecimento e deformação plástica, normalmente empregam juntas de topo, fundindo diretamente ou deformando plasticamente as faces finais de dois condutores. Por outro lado, a brasagem e a soldagem ultrassônica são mais adequadas para juntas sobrepostas, onde um metal de adição ou vibrações ultrassônicas são aplicadas às superfícies sobrepostas para criar uma ligação. Este método de conexão oferece vantagens em aplicações específicas, como quando as espessuras dos condutores variam ou é necessário aumentar a resistência da junta.
Soldagem de topo por flash
A soldagem de topo por flash oferece um método robusto de unir barramentos de alumínio e cobre por meio de ligação metalúrgica. Este processo resulta em um composto intermetálico/Al na interface, proporcionando propriedades mecânicas e elétricas excepcionais. Notavelmente, ele exibe a maior resistência à tração entre os quatro métodos de soldagem, juntamente com baixa resistência à soldagem e aumento mínimo de temperatura, tornando-o ideal para conexões de cobre-alumínio. No entanto, devido aos rigorosos requisitos do ambiente de produção, desafios no controle dimensional e preocupações ambientais, a soldagem de topo a topo geralmente não é recomendada para aplicações onde não é estritamente necessária.
Soldagem por fricção (FSW)
A soldagem por fricção é um processo de união em estado sólido. Durante a soldagem por fricção (FSW), uma ferramenta cilíndrica com um ombro e pino especialmente projetados é girada e inserida na peça de trabalho. O calor de fricção gerado plastifica o material. À medida que a ferramenta atravessa a linha de junta, o material plastificado é mecanicamente agitado e consolidado pela ferramenta, resultando em uma ligação de estado sólido entre metais diferentes, como cobre e alumínio.
Os testes mostraram que o FSW oferece excelentes propriedades de tração e baixa resistência da junta, tornando-o um método de união confiável. O processo é simples e adequado para soldagem de ligas de alumínio nas séries 1000, 6000 e 8000, demonstrando alta eficiência e estabilidade na produção. Portanto, o FSW é uma técnica promissora para unir cobre e alumínio.
Soldagem ultrassônica
A soldagem ultrassônica une condutores de cobre e alumínio combinando a vibração de alta frequência de um sonotrodo e a pressão de um cabeçote de soldagem. Este método é amplamente utilizado para conectar fios a terminais e pode atingir baixa resistência elétrica e alta resistência de ligação.
Os resultados dos testes mostram que a soldagem ultrassônica tem menor resistência de contato e aumento de temperatura, mas a força de ligação pode ser menor. Para barramentos de cobre e alumínio mais finos, a soldagem ultrassônica é confiável, mas para os mais grossos, a energia do equipamento de soldagem pode ser insuficiente, levando a uma soldagem incompleta e redução da força de ligação.
Brasagem
A brasagem de alumínio e cobre requer uma consideração cuidadosa de seus diferentes pontos de fusão (cobre: 1083 ° C, alumínio: 660 ° C). Para garantir que apenas o metal de adição de brasagem derreta e não os metais básicos, deve-se usar fluxo e liga de brasagem apropriados (ponto de fusão entre 850-900 ° C). Ao brasar alumínio e cobre, todos os componentes devem estar limpos. As superfícies podem ser limpas com uma escova de aço ou lixa antes do aquecimento e um fluxo deve ser aplicado para evitar oxidação e contaminação. O fluxo não apenas evita a oxidação da superfície, mas também promove a transferência de calor, garantindo uma forte ligação durante o processo de brasagem.
Devido às diferentes propriedades metálicas do cobre e do alumínio, várias questões precisam ser consideradas durante a soldagem:
1. O cobre e o alumínio têm diferentes coeficientes de expansão térmica e condutividade térmica. Durante o aquecimento, a quantidade de expansão é diferente. Se aquecido lentamente por muito tempo, a diferença na expansão será maior. Portanto, é necessário controlar o aquecimento da superfície de soldagem e o tempo de soldagem durante o processo de soldagem.
2. A junta soldada obtida pela soldagem composta de materiais diferentes de cobre e alumínio tem fragilidade relativamente alta e fases quebradiças são facilmente geradas durante o processo de soldagem. Devido à formação de compostos intermetálicos de cobre-alumínio na junta, principalmente alumínio de cobre, compostos quebradiços são gerados na solda de cobre-alumínio, o que pode facilmente levar a uma diminuição na resistência da solda.
3. Os pontos de fusão de cobre e alumínio diferem muito em cerca de 400 °C. Durante a soldagem, é fácil ter uma situação em que o alumínio derreteu, mas o cobre não foi totalmente penetrado. Portanto, durante a soldagem, geralmente é necessário direcionar diretamente o cobre.
NO.2 Conexões aparafusadas de alumínio a cobre
- Conexões aparafusadas de alumínio para cobre
- Os fixadores geralmente incluem parafusos, porcas, arruelas bipartidas ou arruelas de pressão.
Em conexões aparafusadas entre cobre e alumínio, os sais de cobre podem corroer o alumínio, enquanto os sais de alumínio não corroem o cobre. Para minimizar os efeitos da corrosão eletroquímica e subsequente corrosão do alumínio, o condutor de alumínio deve sempre ser instalado acima do condutor de cobre.
Quando as superfícies bimetálicas de cobre e alumínio foram revestidas (por exemplo, com prata, estanho ou cádmio), geralmente não é necessária nenhuma preparação adicional antes da união. No entanto, se o cobre ou alumínio estiver nu e não revestido, uma quantidade generosa de inibidor de corrosão deve ser aplicada nas superfícies de contato e na junta. Além disso, todas as superfícies de contato não revestidas (sem revestimentos de prata, estanho, cádmio ou cera) devem ser devidamente limpas ou polidas antes da conexão elétrica.
A escolha dos fixadores geralmente depende dos metais específicos que estão sendo unidos. Para condutores de cobre e alumínio, conjuntos de parafusos de liga de alumínio, conjuntos de parafusos de bronze de silício estanhado e conjuntos de parafusos de aço inoxidável são comumente usados.
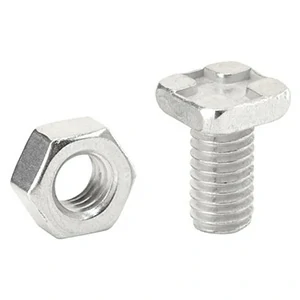
Fixadores de alumínio
Os fixadores de alumínio são comumente usados para unir alumínio a alumínio, alumínio a alumínio estanhado, alumínio a cobre estanhado e cobre estanhado a alumínio estanhado.
Os parafusos de alumínio comerciais padrão são normalmente feitos de liga 2024-T4, mas seu teor de cobre pode levar à corrosão galvânica, tornando-os inadequados para aplicações elétricas externas. A liga de alumínio 6061-T6 oferece resistência comparável ao 2024-T4, mas tem melhor resistência à corrosão, tornando-a a escolha preferida para aplicações elétricas externas.
Além disso, o uso de arruelas planas de aço e arruelas de pressão Belleville de aço pode garantir uma distribuição uniforme da pressão de contato, evitando a concentração de corrente e pontos quentes dentro da conexão.
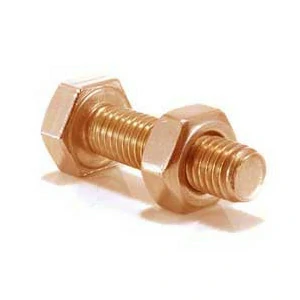
Fixadores de bronze silício
Os fixadores de bronze de silício são comumente usados para unir cobre a cobre, cobre a alumínio estanhado, cobre estanhado a cobre estanhado, cobre a bronze e bronze a bronze. Uma consideração crucial ao usar fixadores de bronze silício é a necessidade de arruelas Belleville de aço inoxidável para gerar e manter efetivamente a força de fixação necessária para uma conexão de baixa resistência.
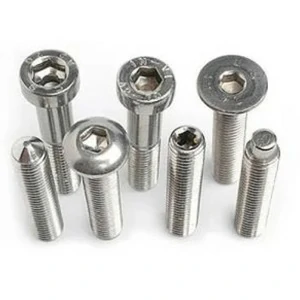
Fixadores de aço inoxidável
A escolha de componente mais econômica e confiável é o aço inoxidável da série 300 (T18-8). Reconhecidos por sua excelente resistência à corrosão e resistência, os fixadores de aço inoxidável são universalmente reconhecidos como um material adequado para todas as aplicações.
É crucial observar que, ao aparafusar os componentes, o torque correto deve ser aplicado para apertar os fixadores. Diferentes tamanhos de parafusos têm valores de torque ideais que produzem a conexão mais confiável e de baixa resistência. Abaixo está uma tabela de valores de torque ideais para vários materiais e tamanhos de parafusos:
Tamanho do parafuso (pol) | Alumínio (ft/lb) | Silício-Bronze (ft/lb) | Aço inoxidável (ft/lb) |
3/8 | 14 | 20 | 20 |
1/2 | 25 | 40 | 40 |
5/8 | 40 | 55 | 55 |
3/4 | 54 | 87 | 87 |
Além disso, para conexões metálicas diferentes, como cobre-alumínio, são necessárias arruelas específicas, como arruelas Belleville, arruelas planas, arruelas de pressão divididas ou arruelas de pressão em estrela.
O tipo específico de fixador é selecionado com base em uma combinação das características mecânicas e elétricas da aplicação. Normalmente, os fixadores não carregam nenhuma carga elétrica; no entanto, a seleção de certas combinações de metais pode reduzir a probabilidade de corrosão e, ao mesmo tempo, fornecer a resistência mecânica necessária para manter a integridade da junta.
Resumir
Em resumo, a união de cobre e alumínio é crucial para aplicações elétricas e mecânicas.
A soldagem e o aparafusamento oferecem vantagens e desvantagens distintas, e o método ideal depende dos requisitos específicos da aplicação.
Técnicas de soldagem, como soldagem de topo por flash, soldagem por fricção e soldagem ultrassônica, fornecem excelente resistência da junta e condutividade elétrica.
As conexões aparafusadas, por outro lado, requerem atenção cuidadosa para evitar corrosão galvânica. A seleção de fixadores e arruelas apropriados é fundamental.
Em aplicações práticas, o método de união mais adequado deve ser escolhido com base em circunstâncias específicas para garantir a segurança e confiabilidade da junta de cobre-alumínio.